摘 要 本次设计是对后钢板弹簧吊耳零件的加工工艺规程及一些工序的专用夹具设计。后钢板弹簧吊零件的主要加工表面是平面及孔。由加工工艺原则可知,保证平面的加工精度要比保证孔的加工精度容易。所以本设计遵循先面后孔的原则。并将孔与平面的加工明确划分成粗加工和精加工阶段以保证加工精度。基准选择以后钢板弹簧吊耳大外圆端面作为粗基准,以后钢板弹簧吊耳大外圆端面与两个工艺孔作为精基准。主要加工工序安排是先以后钢板弹簧吊耳大外圆端面互为基准加工出端面,再以端面定位加工出工艺孔。在后续工序中除个别工序外均用端面和工艺孔定位加工其他孔与平面。整个加工过程均选用组合机床。
关键词 后钢板弹簧吊耳,加工工艺,专用夹具
ABSTRACT The design of the plate after spring lug parts of the processing order of the processes and some special fixture design. Spring plate after hanging parts of the main plane of the surface and pore. By the principle known Processing , the plane guarantee precision machining holes than guarantee the machining precision easy. So the design follows the surface after the first hole principle. Plane with holes and the processing clearly divided into roughing and finishing stages of processing to ensure accuracy. After selecting base plate spring lug large cylindrical face as a rough benchmark, After the leaf spring lug large cylindrical end with two holes as a precision technology benchmarks. main processes arrangements after the first spring plate lug large cylindrical face each other benchmarks machined face, End position to further processing out of holes. In addition to the follow-up processes are individual processes with end-positioning technology and other processing Kong and plane. The entire process of processing machine combinations were selected.
Key words The empress steel plate spring coil mourns the ear,Process the craft,Appropriation tongs
2 后钢板弹簧吊耳加工工艺规程设计 2.1零件的分析 2.1.1零件的作用 题目给出的零件是CA10B解放牌汽车后钢板弹簧吊耳。后钢板弹簧吊耳的主要作用是载重后,使钢板能够得到延伸,伸展,能有正常的缓冲作用。因此汽车后钢板弹簧吊耳零件的加工质量会影响汽车的工作精度、使用性能和寿命。汽车后钢板弹簧吊耳主要作用是减震功能、阻尼缓冲部分功能、导向功能。
1.1.2零件的工艺分析 由后钢板弹簧吊耳零件图知可将其分为两组加工表面。它们相互间有一定的位置要求。现分析如下: (1)以 两外圆端面为主要加工表面的加工面。这一组加工表面包括:。 两外圆端面的铣削,加工 的孔,其中 两外圆端面表面粗糙度要求为 , 的孔表面粗糙度要求为 (2)以 孔为主要加工表面的加工面。这一组加工表面包括:2个 的孔,2个 的孔、2个 孔的内外两侧面的铣削,宽度为4 的开口槽的铣削,2个在 同一中心线上数值为 的同轴度要求。其中2个 的孔表面粗糙度要求为 ,2个 的孔表面粗糙度要求为 ,2个 孔的内侧面表面粗糙度要求为 ,2个 孔的外侧面表面粗糙度要求为 ,宽度为4 的开口槽的表面粗糙度要求为 。 2.2工艺过程设计所应采取的相应措施 由以上分析可知。该零件的主要加工表面是平面及孔系。一般来说,保证平面的加工精度要比保证孔系的加工精度容易。因此,对于该零件来说,加工过程中的主要问题是保证平面的尺寸精度以及孔的尺寸精度及位置精度,处理好孔和平面之间的相互关系。 该类零件的加工应遵循先面后孔的原则:即先加工零件的基准平面,以基准平面定位加工其他平面。然后再加工孔系。后钢板弹簧吊耳的加工自然应遵循这个原则。这是因为平面的面积大,用平面定位可以确保定位可靠夹紧牢固,因而容易保证孔的加工精度。其次,先加工平面可以先切去铸件表面的凹凸不平。为提高孔的加工精度创造条件,便于对刀及调整,也有利于保护刀具。 后钢板弹簧吊耳零件的加工工艺应遵循粗精加工分开的原则,将孔与平面的加工明确划分成粗加工和精加工阶段以保证孔系加工精度。 由于后钢板弹簧吊耳的生产量很大。怎样满足后钢板弹簧吊耳生产率要求也是过程中的主要考虑因素。 2.3后钢板弹簧吊耳加工定位基准的选择 2.3.1 确定毛坯的制造形式 零件材料为Q235。由于生量已达到大批生产的水平,而且零件的轮廓尺寸不大,故可以采用铸造成型,这对提高生产效率,保证加工质量也是有利的。 2.3.2粗基准的选择 粗基准选择应当满足以下要求: (1) 粗基准的选择应以加工表面为粗基准。目的是为了保证加工面与不加工面的相互位置关系精度。如果工件上表面上有好几个不需加工的表面,则应选择其中与加工表面的相互位置精度要求较高的表面作为粗基准。以求壁厚均匀、外形对称、少装夹等。 (2) 选择加工余量要求均匀的重要表面作为粗基准。例如:机床床身导轨面是其余量要求均匀的重要表面。因而在加工时选择导轨面作为粗基准,加工床身的底面,再以底面作为精基准加工导轨面。这样就能保证均匀地去掉较少的余量,使表层保留而细致的组织,以增加耐磨性。 (3) 应选择加工余量最小的表面作为粗基准。这样可以保证该面有足够的加工余量。 (4) 应尽可能选择平整、光洁、面积足够大的表面作为粗基准,以保证定位准确夹紧可靠。有浇口、冒口、飞边、毛刺的表面不宜选作粗基准,必要时需经初加工。 (5) 粗基准应避免重复使用,因为粗基准的表面大多数是粗糙不规则的。多次使用难以保证表面间的位置精度。 为了满足上述要求,基准选择以后钢板弹簧吊耳大外圆端面作为粗基准,先以后钢板弹簧吊耳大外圆端面互为基准加工出端面,再以端面定位加工出工艺孔。在后续工序中除个别工序外均用端面和工艺孔定位加工其他孔与平面。
本章主要是对后钢板弹簧吊耳的加工工艺进行设计。先要明确零件的作用 ,本次设计的后钢板弹簧吊耳的主要作用就是载重后,使钢板能够得到延伸,伸展,能有正常的缓冲作用。确定了零件的机械加工余量、工序尺寸及毛坯尺寸后,就可以对零件的工艺路线进行分析,制定出几套工艺方案,然后对这几套方案进行分析比较,选择最优方案,最后进行时间定额计算及生产安排。优良的加工工艺是能否生产出合格,优质零件的必要前提,所以对加工工艺的设计十分重要,设计时要反复比较,选择最优方案。
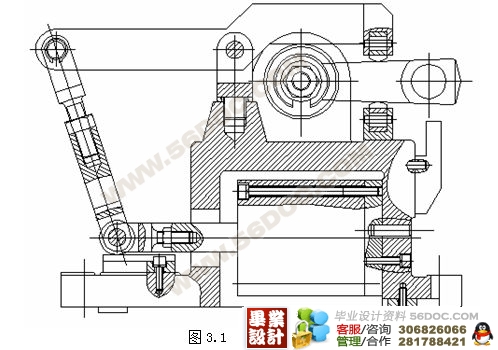
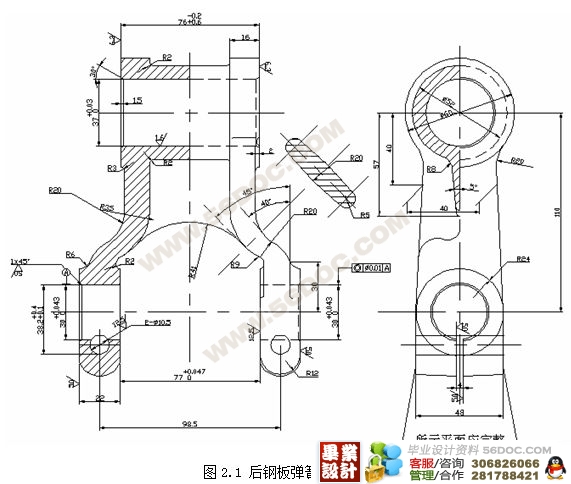
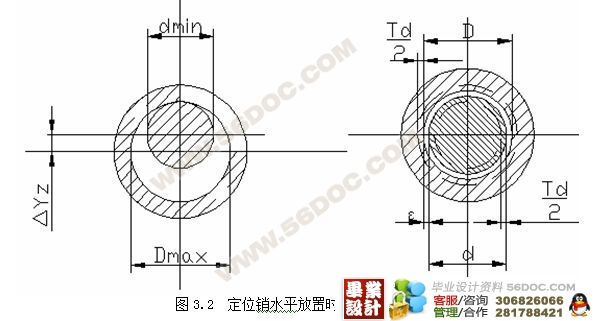
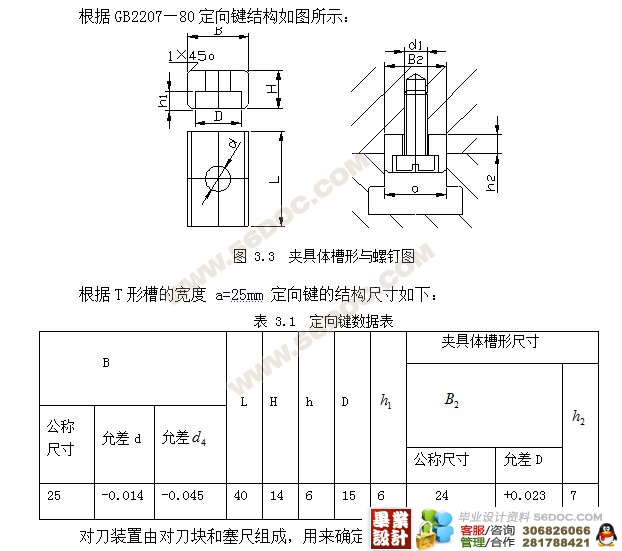
目 录
摘 要 Ⅰ ABSTRACT II 目录 1 1绪 论 1 2 后钢板弹簧吊耳加工工艺规程设计 3 2.1零件的分析 3 2.1.1零件的作用 3 1.1.2零件的工艺分析 3 2.2工艺过程设计所应采取的相应措施 4 2.3后钢板弹簧吊耳加工定位基准的选择 4 2.3.1 确定毛坯的制造形式 4 2.3.2粗基准的选择 4 2.3.3精基准的选择 5 2.4 工艺路线的制定 5 2.4.1 工艺方案一 5 2.4.2 工艺方案二 5 2.4.3 工艺方案的比较与分析 6 2.5机械加工余量、工序尺寸及毛坯尺寸的确定 6 2.6确定切削用量及基本工时(机动时间) 7 2.7时间定额计算及生产安排 16 2.8 本章小结 18 3 粗铣后钢板弹簧吊耳内侧端面夹具设计 19 3.1粗铣后钢板弹簧吊耳内侧端面夹具设计 19 3.2定位方案的分析和定位基准的选择 19 3.3定位误差分析 19 3.4铣削力与夹紧力计算 20 3.5定向键与对刀装置设计 21 3.6夹紧装置及夹具体设计 23 3.7夹具设计及操作的简要说明 24 3.8本章小结 24 4 加工 工艺孔夹具设计 25 4.1加工 工艺孔夹具设计 25 4.2定位方案的分析和定位基准的选择 25 4.4切削力的计算与夹紧力分析 26 4.5钻套、衬套、钻模板及夹具体设计 26 4.6夹具精度分析 28 4.7夹具设计及操作的简要说明 28 4.8本章小结 29 5 加工 工艺孔夹具设计 30 5.1加工 工艺孔夹具设计 30 5.2定位方案的分析和定位基准的选择 30 5.3定位元件的设计 30 5.4定位误差分析 32 5.5切削力的计算与夹紧力分析 32 5.6钻套、衬套、钻模板及夹具体设计 32 5.7夹具精度分析 34 5.8夹具设计及操作的简要说明 34 5.9本章小结 35 结 论 36 参 考 文 献 37 致 谢 38 |