座椅摇臂冲孔复合模设计(含CAD零件图和装配图)
来源:wenku163.com 资料编号:WK16310640 资料等级:★★★★★ %E8%B5%84%E6%96%99%E7%BC%96%E5%8F%B7%EF%BC%9AWK16310640
资料介绍
座椅摇臂冲孔复合模设计(含CAD零件图和装配图)(论文说明书18000字,CAD图纸11张)
3设计方案
3.1 零件的工艺分析
图1所示零件,材料为Q235钢,料厚2.0mm,零件上有3个圆孔,外形为不规则形状。零件形状较为复杂,材料为结构钢,硬度较低,大批量生产。
图3.1零件图
3.2 零件成型工艺分析与排样设计
3.2.1 成型工艺分析
根据该工件的形状、尺寸以及技术要求,综合考虑可以有以下三种方案:
方案一:落料,冲孔两套单工序模生产;
方案二:落料+冲孔一套复合模。1套单工序模生产;
方案三:冲导正销孔;冲3个圆孔,空工位;冲裁废料、冲裁废料、空工位;切断(将零件从载体上切下),采用1道7工位级进模生产。
三种方案比较见下表2.1
表3.1 三种方案的比较
模具种类
比较项目 单工序模 复合模 级进模
冲件精度 较低 可达IT10-IT8 可达IT13-IT10
生产效率 较低 冲件被顶到模具工作表面上 工序间自动送料,可以自动排除制件,生产效率高
生产批量 适合大、中、小批量 适合大批量 适合大批量
模具复杂程度 较易 较复杂 复杂
模具成本 较低 较高 高
模具制作精度 较低 较高 高
模具制造周期 较快 较长 长
模具外形尺寸 较小 中等 较大
冲压设备能力 较小 中等 较大
工作条件 一般 较好 好
方案一模具结构简单,但需要模具数量多,生产率较低,误差大,而且效率低,不满足大批量生产的要求。方案三,采用一套级进模,生产效率高,但给个工序间易发生干涉状况,会对品质造成影响。方案二采用一套复合模具,形位精度比方案一与二都高,且生产率也可以满足大批量生产的需要。为此,落料+冲孔一套复合模。1套单工序模生产,生产效率高的同时也能保证零件的精度。
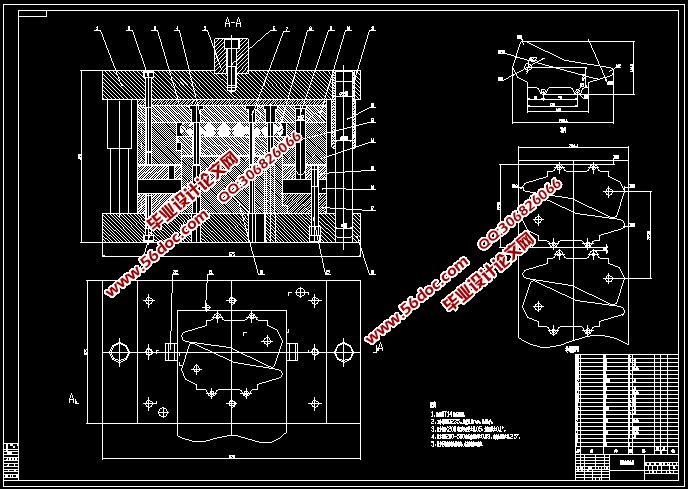
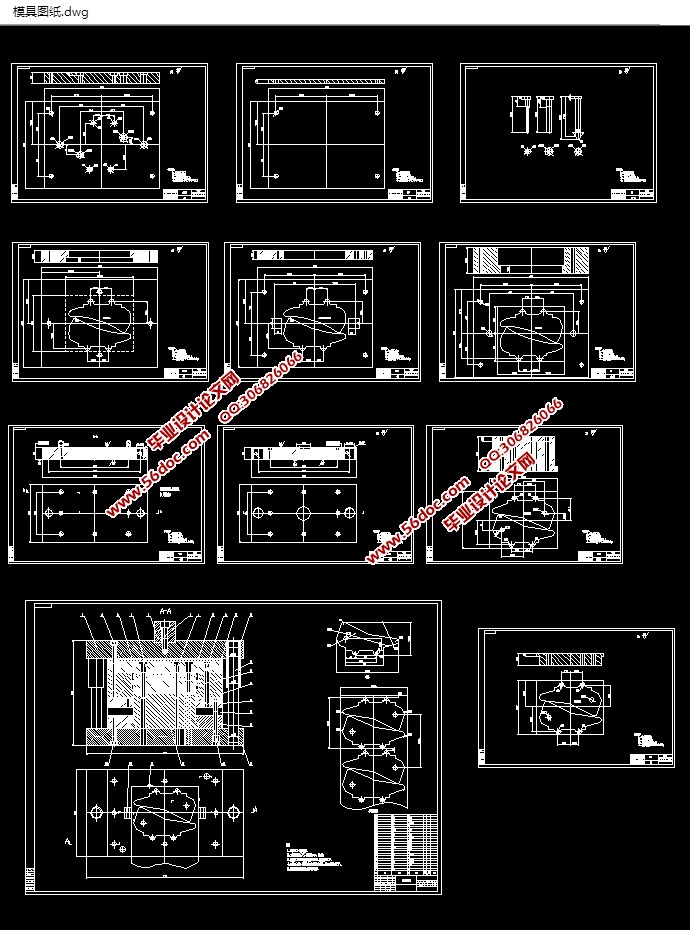
目 录
1、摘要…………………………………………………………………………………………3
2、概论…………………………………………………………………………………………5
2.1模具行业发展前景分析…………………………………………………………………5
2.2模具行业发展趋势简要分析……………………………………………………………5
2.3冲压的概念、特点及应用………………………………………………………………7
2.4 冲压的基本工序及模具 ………………………………………………………………8
2.5 冲压技术的现状及发展方向 …………………………………………………………9
3、设计方案 …………………………………………………………………………………13
3.1 零件的工艺分析 ………………………………………………………………………13
3.2 零件的成型工艺分析与排样设计 ……………………………………………………13
3.3冲裁排样设计………………………………………………………………………….14
3.3.1产品尺寸的展开………………………………………………………………….14
3.3.2冲裁排样方案的确定……………………………………………………………15
3.4 搭边的选取…………………………………………………………………………….15
3.5送料步距、条料宽度及板料间距计算……………………………………………….16
3.5.1 送料步距………………………………………………………………………….16
3.5.2 条料宽度及板料间距的计算…………………………………………………….17
3.6零件排样……………………………………………………………………………….17
3.7 各工序的确定………………………………………………………………………….18
3.8 冲裁力和压力中心的计算…………………………………………………………….19
3.8.1 冲裁力及辅助力..……………………………………………………………….19
3.8.2 冲孔力的计算..………………………………………………………………….20
3.8.3 冲孔卸料力的计算..…………………………………………………………….21
3.8.4 冲孔推件力的计算..…………………………………………………………….21
3.8.5 压力中心的计算………………………………………………………………….21
3.9刃口尺寸的计算……………………………………………………………………….22
3.9.1落料刃口尺寸计算………………………………………………………………24
3.10冲裁模主要零部件的结构与设计…………………………………………………….25
3.10.1 模具类型的选择 ……………………………………………………………….25
3.10.2 定位方式的选择 ……………………………………………………………….25
3.10.3 卸料装置和推件装置的选择 …………………………………………………26
3.11 工作零件的设计………………………………………………………………………28
3.11.1凹模的设计 ……………………………………………………………………28
3.11.2凸凹模的设计……………………………………………………………………29
3.11.3凸模的设计………………………………………………………………………30
3.11.4 模架及组成零件的设计…………………………………………………………32
3.12 压力机的选取及校核………………………………………………………………….33
3.12.1压力机的选择 …………………………………………………………………33
3.12.2装模高度的校核 ……………………………………………………………….33
3.13.总组装图……………………………………………………………………………….34
3.14 模具材料的选用……………………………………………………………………….34
3.15模具的装配与检测…………………………………………………………………….35
3.15.1 模具的装配 …………………………………………………………………….35
3.15.2模具的检测 …………………………………………………………………….36
总 结 ………………………………………………………………………………………….37
致 谢 ………………………………………………………………………………………….39
参考文献……………………………………………………………………………………….40
|